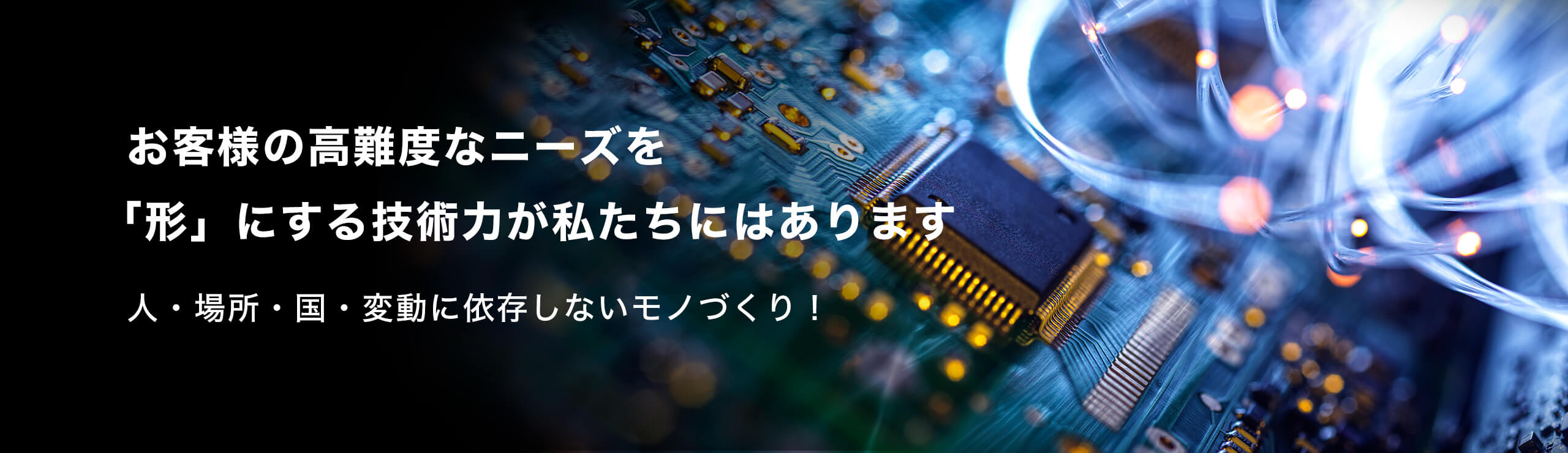
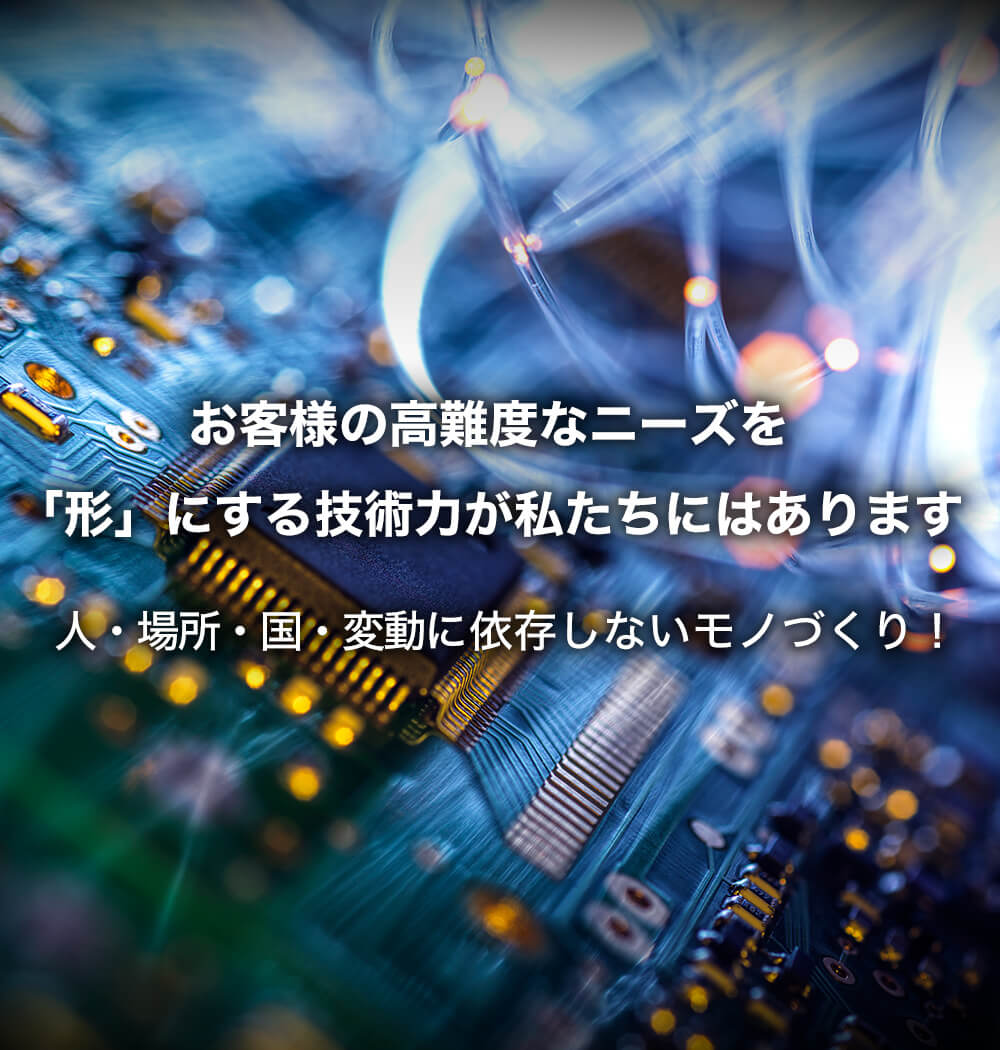
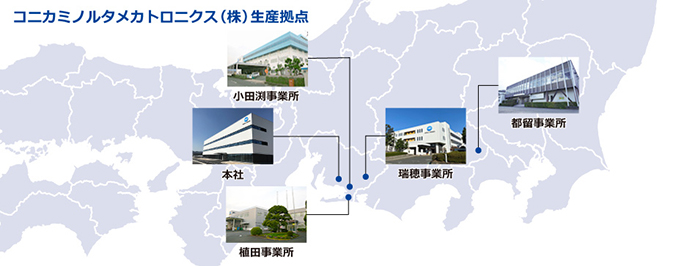
事業紹介
コニカミノルタメカトロニクスでは、光学機器や電子機器の組立製造やプリント基板のパターン設計・試作・実装などをお請けしております。また精密金型や治具、組立自動機の設計製作から樹脂成形や板金加工などによる各種精密加工部品の製造まで承っています。
新着情報
- 2023年4月3日ニュース
- 次期中期計画の戦略実行に向け事業領域ごとに会社分割しました
- 2021年10月29日動画公開
- コニカミノルタメカトロニクスは、コニカミノルタYouTubeチャンネル上において
コニカミノルタメカトロニクス本社「Digital Manufacturing Center MIKAWAオープン」の動画を公開いたしました。
【「Digital Manufacturing Center MIKAWAオープン」 - YouTube】 - 2021年3月16日ニュース
- コニカミノルタメカトロニクス本社の竣工式を執り行いました
- 2019年4月1日ニュース
- コニカミノルタ生産子会社3社が合併しました